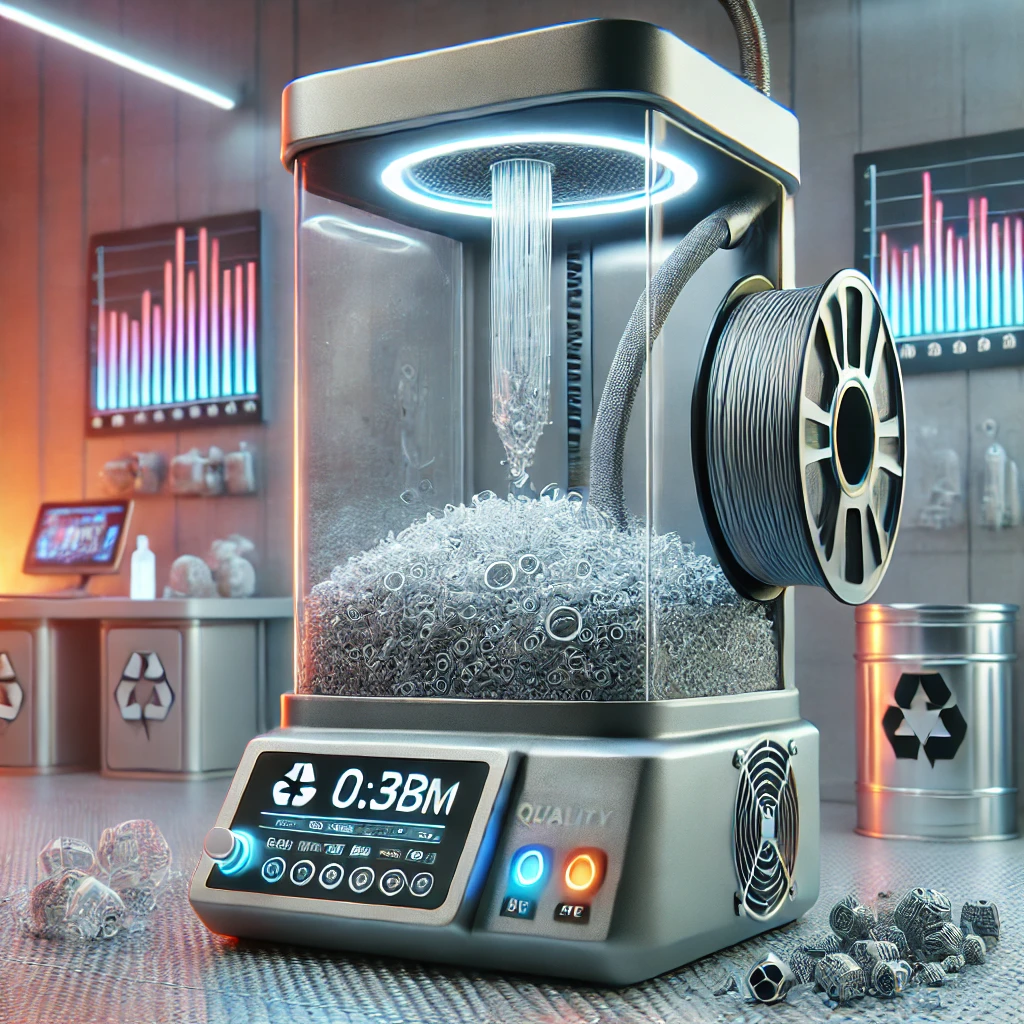
Introduction
The increasing accumulation of plastic waste is a major environmental concern. Traditional disposal methods such as landfilling and incineration contribute to pollution and greenhouse gas emissions. Recycling plastic waste into 3D printing filament presents an innovative and sustainable solution, reducing environmental impact while promoting a circular economy. This project focuses on developing a machine that converts plastic waste into usable 3D printing filament.
Statement of Problem
Plastic waste is one of the most persistent pollutants, taking centuries to decompose. Existing recycling methods are not sufficient to handle the growing volume of plastic waste, and improper disposal leads to land and marine pollution. Additionally, 3D printing filament is expensive, limiting its accessibility. This project aims to provide an affordable and efficient method for recycling plastic waste into high-quality 3D printing filament.
Abstract
This project involves designing and building a machine that transforms plastic waste into 3D printing filament. The machine first shreds plastic waste into small pieces, melts it at a controlled temperature, and extrudes it into a filament of consistent diameter. The study evaluates the efficiency, cost-effectiveness, and feasibility of this recycling method. By providing a sustainable way to repurpose plastic, the project contributes to waste reduction and promotes eco-friendly 3D printing.
Objectives
- To develop a cost-effective machine for converting plastic waste into 3D printing filament.
- To assess the feasibility and efficiency of recycling different types of plastics.
- To produce high-quality filament that can be used in standard 3D printers.
- To promote environmental sustainability by reducing plastic waste.
Apparatus
- Plastic waste (PET, PLA, ABS)
- Plastic shredder
- Extruder with temperature control
- Heating chamber
- Cooling system (water bath or air cooling)
- Diameter measurement sensor
- Spool winder
- Power supply
Procedure
- Collection and Sorting – Collect different types of plastic waste and sort them based on their properties (e.g., PET, PLA, ABS).
- Shredding – Feed the plastic into a shredder to obtain small, uniform pieces.
- Melting and Extrusion – Heat the plastic at an optimal temperature to achieve a molten state and extrude it through a nozzle.
- Cooling and Solidification – Pass the extruded filament through a cooling system to harden it.
- Diameter Control – Use sensors to maintain a consistent filament diameter.
- Spooling – Wind the cooled filament onto a spool for storage and use in 3D printing.
Data Collected
- Types and quantities of plastic processed
- Temperature settings for optimal melting
- Filament diameter consistency (measured at intervals)
- Production speed (length of filament produced per hour)
- Comparison of filament quality with commercial products
Observations
- Different types of plastic require specific temperature settings for optimal extrusion.
- Consistency in filament diameter improves with proper cooling and speed control.
- Recycled filament performs well in standard 3D printers when properly processed.
- PLA and PET yield better filament quality compared to ABS due to lower melting inconsistencies.
Conclusion
The project successfully demonstrates the feasibility of converting plastic waste into 3D printing filament. The machine effectively processes plastic waste, producing a filament suitable for 3D printing. This approach provides a sustainable recycling method while reducing plastic pollution. However, fine-tuning the extrusion process is necessary to ensure uniform filament quality.
Recommendation
- Improve temperature regulation to enhance filament consistency.
- Test additional types of plastic to expand the range of recyclable materials.
- Implement automation features to optimize the filament production process.
- Collaborate with recycling centers and makerspaces to promote adoption of the technology.
- Conduct further research on chemical treatments to improve the quality of recycled filament.